東莞馬赫數(shù)控沖床加工課堂 數(shù)控轉(zhuǎn)塔沖床加工過程中工件變形的問題分析
東莞馬赫題記: 隨著鈑金產(chǎn)品更新?lián)Q代的速度加快,傳統(tǒng)的鈑金加工設(shè)備無法滿足生產(chǎn)柔性化要求,數(shù)控鈑金加工設(shè)備在生產(chǎn)中迅速普及。在各種數(shù)控鈑金設(shè)備中,數(shù)控沖床具有加工范圍大,柔性化程度高,成本低的特點,在鈑金加工中應(yīng)用得最為普及。在數(shù)控沖床加工過程中經(jīng)常會遇到工件加工變形的情況,特別是在工件中孔、筋、槽較多時,工件變形尤為嚴重。圖1所示工件加工后常產(chǎn)生扭曲變形,必須增加后續(xù)整形工序,費時費力。
1 工件特點分析
分析圖1中2種工件的異同:工件1的中間部位材料被完全切除掉,只留四邊細邊框;工件2的兩邊部位材料被大量切除掉,方孔之間僅以幾道細筋連著,中間部位密密麻麻分布著散熱孔。這2種工件有個共同點,就是加工過程中有大量的材料從毛坯中切除。
2 加工過程分析
以工件1為例,數(shù)控沖床的常用加工編程軌跡:第一步用修邊刀修整板材基準邊平整垂直(修邊過程見圖2);第二步再進行正式的零件加工,先沖孔,次沖內(nèi)圓弧,再用方?jīng)_頭把中間部位材料打碎掏空,最后切邊刀把零件切下。最后一道工序一般由2個工人配合操作,一個工人負責操控機床,另一個工人守候在沖頭邊,機器切完最后一刀后,機床暫時停頓,工件從毛坯板脫落,工人用鑷子或鉤子把工件取下來。操作機器的工人再啟動機床切第2個工件,周而復始,直到把工件全部加工完成。沖裁過程中卸料板懸空,距離板面0.5 mm左右。這種編程方法排料時工件和工件之問只留切刀寬度,切邊時同時切出相鄰工件的鄰邊輪廓,加工速度快,節(jié)約材料,但是加工出來的零件嚴重扭曲變形。技術(shù)人員取消方?jīng)_頭打碎掏空中間部位這一步驟,只加工圓孔和外輪廓。加工出來的零件變形相對于前一種零件則小得多。從而得出結(jié)論:打碎掏空中間材料是引起加工變形的重要原因。圖3為沖裁過程圖形模擬。
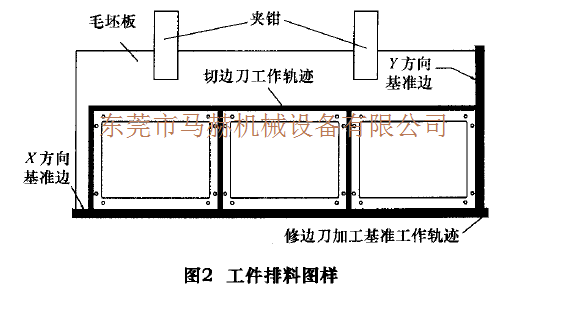
沖裁由凸模和凹模完成,凸模和凹模組成一組刃口,把材料壓在中間,凸模逐步靠近凹模,使材料分離。整個過程可以分成3個階段(見圖4)。
(1)彈性變形階段:由于凸模所施加的壓力,材料產(chǎn)生彈性彎曲并略有擠入凹模口。在這一階段,若板材應(yīng)力沒有超過材料的彈性極限時,當凸模卸載后,材料立刻恢復原狀。
(2)塑性變形階段:材料受力已超過彈性限度。這時凸模擠入材料,同時材料也擠入凹模,由于材料反抗凸模及凹模的擠入,產(chǎn)生彎矩,在彎矩 作用下材料彎曲。這時已經(jīng)有微小裂紋發(fā)生。
(3)剪裂階段:隨著凸模繼續(xù)下行,已形成的上、下微小裂紋將逐漸擴大,并向材料內(nèi)部發(fā)展,當上、下裂紋相遇重合時,材料便開裂分離;完成整個沖裁工作。在彈性變形階段和塑性變形階段材料都產(chǎn)生扭矩使材料變形,塑性變形階段產(chǎn)生的是永久變形。在工件1的加工過程中加工中問方框時采用的是方?jīng)_頭打碎的方式,沖擊次數(shù)太多,再加上工件的邊框和筋都很細,沖裁產(chǎn)生的扭矩使得板材產(chǎn)生的變形量很大。由此可見,減少加工過程中的沖擊次數(shù)和預防扭矩力變形是解決加工變形的主要途徑。